additive manufacturing charpy impact testing|Crystallographic orientation dependence of Charpy impact : mail order Additive manufacturing processes play a disruptive role in several industrial sectors. Among them, wire arc additive manufacturing (WAAM) is a very promising process for the production of large-scale steel components and structures. . it will be proposed a clear strategy to perform and report the Charpy impact testing in WAAM parts. 2 . 27 de jan. de 2024 · About Press Copyright Contact us Creators Advertise Developers Terms Privacy Policy & Safety How YouTube works Test new features NFL Sunday .
{plog:ftitle_list}
Assista vídeos pornô de Bunduda Gostosa de graça, aqui no Pornhub.com. Descubra a crescente coleção de vídeos e filmes Mais relevantes explícitos em alta qualidade. Nenhum outro site pornô é mais popular e tem mais cenas de Bunduda Gostosa do que o Pornhub! Navegue pela nossa incrível seleção de de vídeos pornô em HD em qualquer dispositivo .
Charpy impact testing was performed using a Tinius Olsen model 74 universal impact tester under RT (~293 K) and LNT (~77 K). For each crystallographic direction at a .Additive manufacturing is a robust process for building complex parts with improved mechanical properties. However, if a problem occurs during manufacturing, the produc- tion batch will .A recent work on fatigue properties of maraging steel (Hermann Becker and Dimitrov 2016) and charpy impact properties on some of those metals from selective laser melting (SLM), .
Additive manufacturing processes play a disruptive role in several industrial sectors. Among them, wire arc additive manufacturing (WAAM) is a very promising process for the production of large-scale steel components and structures. . it will be proposed a clear strategy to perform and report the Charpy impact testing in WAAM parts. 2 .
To study the manufacturability and mechanical properties of a low alloy heat treatable medium carbon steel by additive manufacturing, 42CrMo4 (AISI4140) specimens were manufactured by laser powder bed fusion. Influences of processing parameters on relative density and crack density were investigated. Moreover, Charpy impact tests, microhardness, and . Additive manufacturing (AM) is attracting growing interest from various industries due to its ability to fabricate customized and complex components, . Charpy impact testing was performed using a Tinius Olsen model 74 universal impact tester under RT (~293 K) and LNT (~77 K). For each crystallographic direction at a certain temperature, six . Additive manufacturing (AM) . This study selected the impact strength obtained from the Charpy impact test applied to the FDM-produced tough PLA specimen groups as the performance characteristic. High Charpy impact strength will ensure that the specimens are stable against an impact; thus, “larger is better” was chosen as the quality .
Charpy impact test Additive manufacturing L-PBF process Inconel 718 Mechanical properties Microstructure abstract Additive manufacturing is a robust process for building complex parts with improved mechanical properties. However, if a . Semantic Scholar extracted view of "Tension and Charpy V-notch impact properties of wire arc additively manufactured ER80S-Ni1" by Hannah D. Kessler et al. . (DED), as an additive manufacturing technology, has shown unique advantages in multi-material additive manufacturing and remanufacturing. . Structural Testing and Design of Wire Arc .cracks. An estimate for fracture toughness based on Charpy impact absorbed energy is also given. Keywords: Charpy impact test; GMAW; additive manufacturing; secondary cracks 1. Introduction Additive manufacturing can be used to create a near-net shape for complex parts using the layer-by-layer deposition method. For this reason, in this study, Charpy impact behaviour of AM AlSi10Mg samples produced by laser additive manufacturing was accurately investigated. The effect of T6 (solution, quenching and ageing) heat treatment and Hot Isostatic Pressing (HIP) was also evaluated in order to better characterize the material performance and its possible .
The work here demonstrates the need for materials testing standards that are specific to additive manufacturing technologies; as well as concluding that all-printed impact test specimens may offer .
Performance evaluation of Charpy impact tests to investigate

Additive manufacturing, Hot Isostatic Pressing, impact toughness, instrumented Charpy tests, miniaturized Charpy specimens, Ti-6Al-4V. . Lucon, E. and Hrabe, N. (2017), Instrumented impact testing of miniaturized Charpy specimens of AM Ti 6Al 4V, Symposium on Fatigue and Fracture of Additive Manufactured Materials and Components, Atlanta, GA . Additive manufacturing (AM) has revolutionized the manufacturing sector, particularly with the advent of 3D printing technology, which allows for the creation of customized, cost-effective, and waste-free products. However, concerns about the strength and reliability of 3D-printed products persist. This study focuses on the impact of three crucial variables—infill .
stick drop test results
Impact testing is commonly performed using methods such as the Charpy and Izod tests, which involve striking a notched specimen with a swinging pendulum to measure energy absorption. The results of impact testing help in selecting materials for applications where resistance to sudden forces is crucial, such as in construction, automotive, and .KEYWORDS: Steel, Additive manufacturing, Impact, Fatigue INTRODUCTION . Charpy impact test as a commonly used . conditions are kept same. Table 1 covered several preliminary studies on charpy impact energy of AM materials including 316L (Yasa, Deckers et al. 2010, Zhong, Liu et al. 2016, Brytan 2017), . Laser-based metal additive manufacturing has the potential to be applied in the production of parts for safety-critical applications (e.g., aircraft components, armor and military applications), where materials must be able to absorb energy before breaking. Charpy impact testing is a standardized method used to assess the toughness of metals.
The process is repeated layer after layer until the 3D model is complete. The Charpy and Izod impact tests are used to determine the object's hardness, surface roughness, and impact strength. The Charpy test specimen ASTM A370 (Fig. 3) and the Izod test specimen ASTM D256 (Fig. 4) were used. In the present study, instrumented impact strength tests were carried out on Charpy AlSi10Mg samples produced using laser additive manufacturing in order to accurately investigate the influence of . At present, the methods to improve the toughness of alloys include adjustment of alloy composition [21], heat treatment [22], and TWIP.According to Hrabe et al. [23], an increase in the α lath thickness contributed to a higher Charpy impact absorbed energy after the EBM TC4 alloy was annealed in the α+β region.Changfu Li et al. [24] claimed that fracture toughness of .
Impact and fatigue characteristics of additively manufactured
The most common testing method to obtain this property is the Charpy impact test, which measures the energy absorbed by a material during the fracture of a specimen [Citation 7]. Although achieving high-quality parts is possible, the complexity of the parametric setup makes it challenging to anticipate material qualities precisely before .2 ASTM E2248-15, “Standard Test Method for Impact Testing of Miniaturized Charpy V-Notch Specimens,” ASTM Book of Standards, Vol. 03.01, ASTM International, West Conshohocken, PA, 2015. . Nominal dimensions for RHS Charpy specimens. Additive manufacturing was performed with the following parameters: accelerating voltage 60 kV, layer .
Charpy impact testing. Room temperature Charpy impact tests were also conducted at the USNA. . All testing to date indicates that Alloy 625 produced by additive manufacturing using the laser powder-bed process with a post-build stress-relief heat treatment but without HIP demonstrates properties similar to, or better than wrought material. . Additive manufacturing (AM) is attracting growing interest from various industries due to its ability to fabricate customized and complex components, which are difficult to process by traditional methods [1], [2]. . was systematically investigated using instrumented Charpy impact testing. The results demonstrated that the AB(as-built)-LPBF .
In this study, the Metal Arc Gas Welding (GMAW) process was used to develop Wire Arc Additive Manufacturing (WAAM) of austenitic Stainless Steel 316 L. . The specimens utilised for the Charpy impact test were prepared in accordance with the ASTM E23 – 02a standard and which is shown in the Fig. 5. The impact test was conducted under ambient .
3D printing is an additive manufacturing technique (AM) widely used in the aerospace, shipbuilding, automotive and civil construction sectors to obtain lightweight sandwich structures made with complex core shapes to achieve excellent multifunctional properties, such as flexural stiffness, and high energy-absorption capabilities. This study shows an experimental . Additive Manufacturing (AM) has been defined as the process of joining materials to make parts from a 3-dimensional model data one layer at a time . ASTM D256 (for Izod Impact Test) and ASTM D6110 (for Charpy Impact Test) are methods to measure the impact resistance of notched plastic specimens using pendulum-type hammers [[101], [102]].
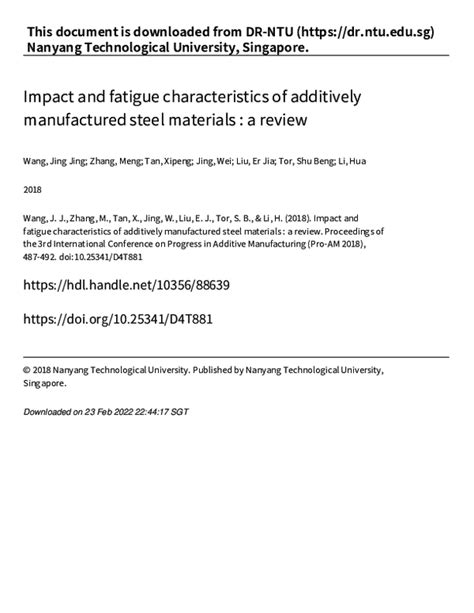
The mechanical properties of the printed structure were analyzed by room temperature tensile testing, Charpy impact test and microhardness measurements in both scanning and build directions. . Arc-based additive manufacturing processes have several advantages over laser-based AM routes, including high deposition rate, high-efficiency energy .An estimate for fracture toughness based on Charpy impact absorbed energy is also given. Keywords: Charpy impact test; GMAW; additive manufacturing; secondary cracks 1. Introduction Additive manufacturing can be used to create a near-net shape for complex parts using the layer-by-layer deposition method.
Additive Manufacturing; Big Data and Sensors; Coating and Surface Engineering; Electrification; Industry 4.0; Inspection and Testing; Welding, Joining and Cutting; Equipment Directory; Public Funded Projects; Services and Support. . The Charpy impact test, also known as the Charpy V-notch test, is a high strain-rate test that involves .
Crystallographic orientation dependence of Charpy impact

stick drop test score example
stock note 10 screen protector drop test
ICQ New: Se vale tudo
additive manufacturing charpy impact testing|Crystallographic orientation dependence of Charpy impact